Sculpteo, a leader in 3D printing, has been awarded the ISO 13485 certification by the Association Française de Normalisation (AFNOR) for its excellence in medical device manufacturing. This milestone enables the company to enhance its presence in the healthcare sector with customized, patient-friendly medical products.
ISO 13485 sets stringent criteria for quality control systems applied to medical devices, ensuring full traceability and control of manufacturing processes. The certification covers various medical device classes, each with specific risk levels from Class I to Class III.
ISO 13485 Classes
Class I | Class IIa | Class IIb | Class III |
Lowest risk class | Moderate/measured risk potential | High/important risk potential | Highest risk class |
Prosthesis covers, corrective eyeglasses, vehicles for disabled people, crutches | Certain prosthesis fittings, contact lenses, ultrasound equipment, dental crowns | Condoms and contacts disinfectants | Breast implants, stents, hip prostheses, |
French company Sculpteo which provides on-demand 3D printing for startups and SMEs covers classes I and IIa. Founded in 2009 by Eric Carreel and Clément Moreau, the company was acquired by BASF New Business GmbH in 2019 and is currently led by Alexandre d’Orsetti.
MedicalExpo e-magazine contacted Alexandre d’Orsetti CEO of Sculpteo to know more about the outcomes of this new certification, what it means for Sculpteo in terms of market expansion and partnerships, and how the company plans to collaborate with healthcare professionals.
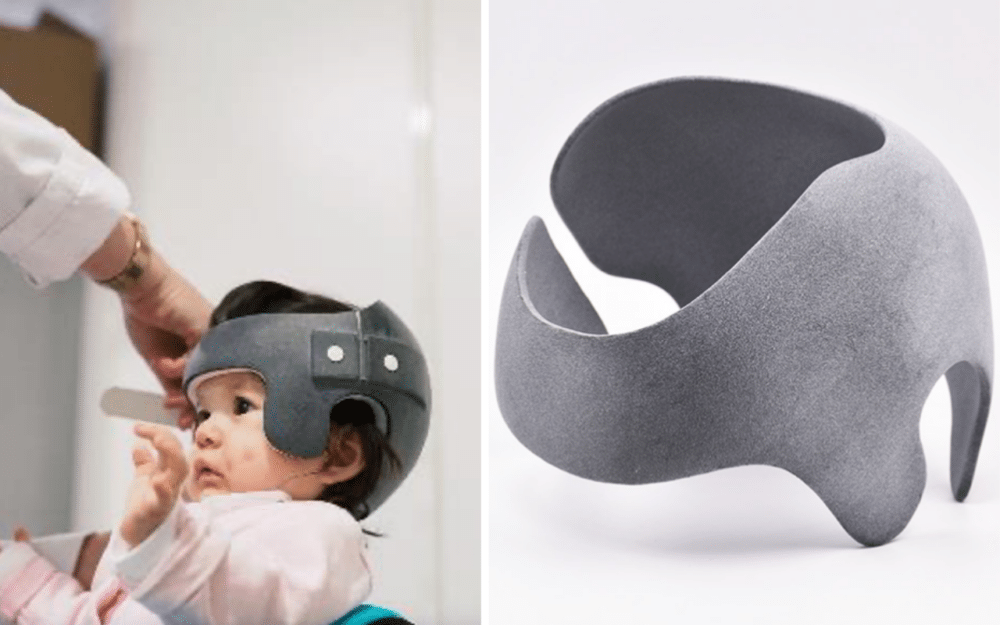
What products are concerned with this certification?
Alexandre d’Orsetti: “Sculpteo’s ISO 13485 certification covers a range of 3D-printed medical components designed to meet the highest standards of quality and safety. These products include surgical guides and tooling, orthopedic parts such as braces or helmets, custom prosthetics, dental devices, and even special equipment such as housings and mechanical parts.”
In what materials are they manufactured?
Alexandre d’Orsetti: “We utilize biocompatible materials such as medical-grade polymers and metals.”
For which patients and which pathology are they intended?
Alexandre d’Orsetti: These devices are intended for patients requiring surgical interventions, dental corrections, orthopedic support, or prosthetic limbs, addressing pathologies like bone fractures, dental misalignments, limb loss, and other medical conditions necessitating precise and customized medical solutions.
What opportunities does this milestone open up for Sculpteo in terms of market expansion and partnerships?
Alexandre d’Orsetti: “Achieving ISO 13485 certification significantly expands Sculpteo’s market opportunities by enabling us to dive deeper and compete in the global medical device market. We were already very active in this sector, but it will open doors for partnerships with hospitals, clinics, dental practices, and orthopedic centers looking for reliable and certified 3D-printed solutions. Additionally, this certification enhances our appeal to medical device manufacturers seeking to outsource high-quality components, thereby fostering collaborations that can drive innovation and efficiency in medical technology.”
How does achieving the ISO 13485 certification align with Sculpteo’s long-term strategic goals?
Alexandre d’Orsetti: “Obtaining ISO 13485 certification is a crucial step in Sculpteo’s strategic plan to establish itself as a leader in the medical 3D printing industry, which is one of our key segments. It aligns with our long-term goals by ensuring we meet the stringent regulatory requirements necessary for producing components for medical devices, thereby boosting our credibility and trust with healthcare providers and patients. This sector has been growing at a steady pace for many years, and this certification supports our mission to provide cutting-edge, customized medical solutions, ensuring patient safety and improving healthcare outcomes.”
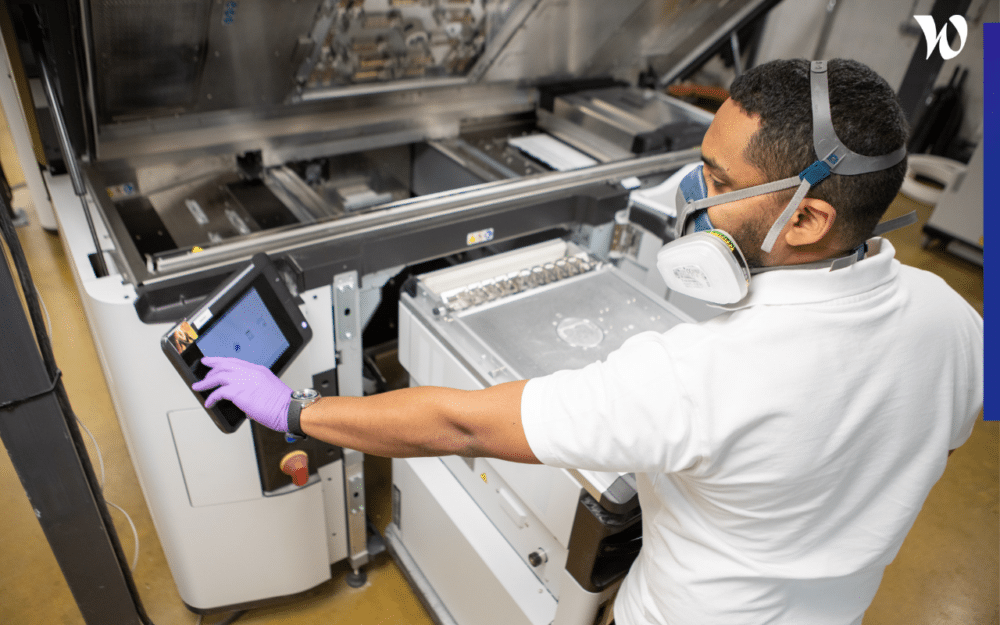
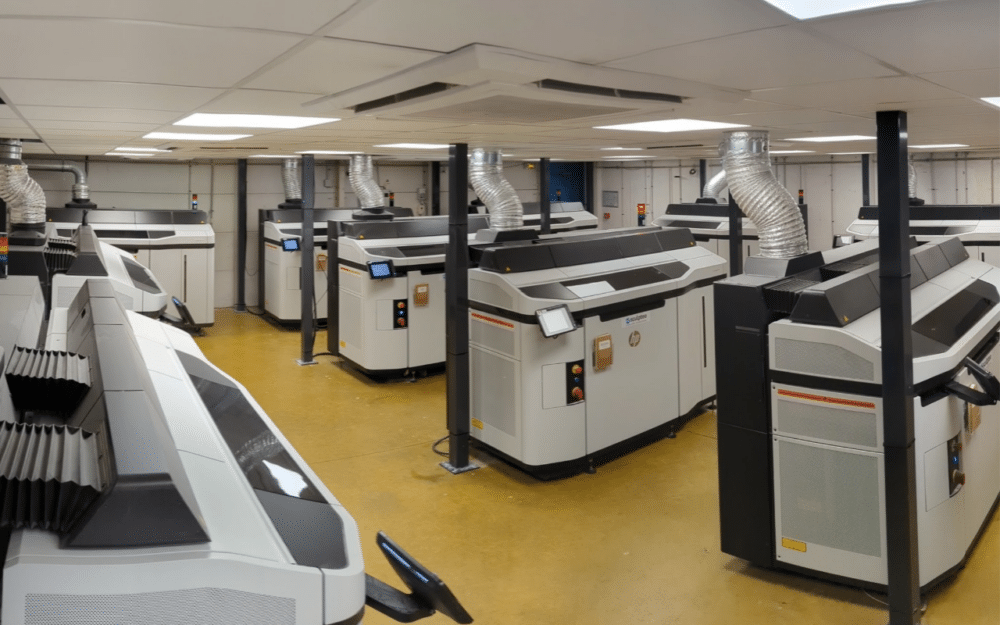
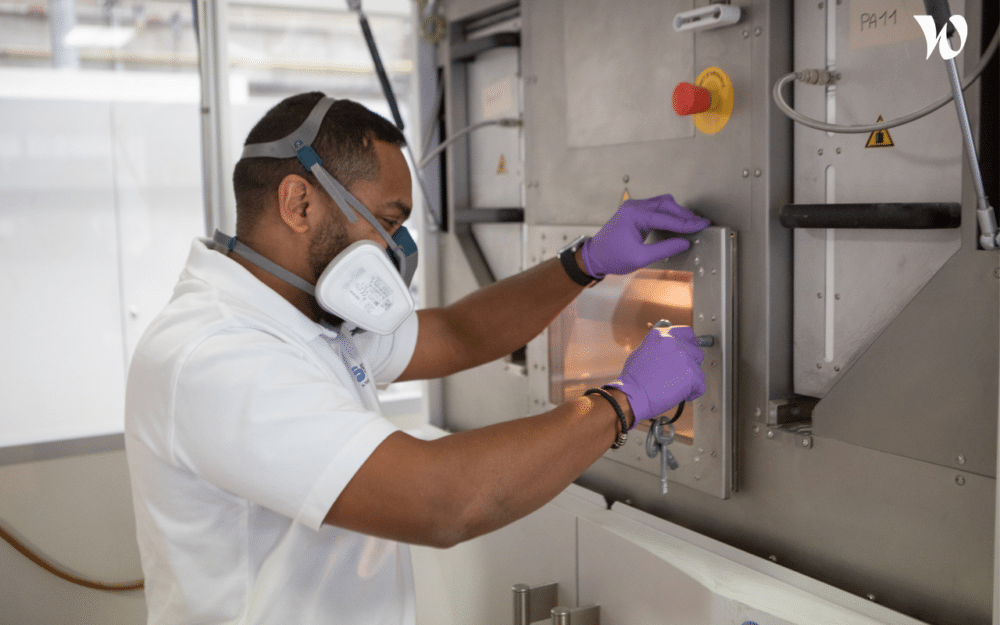
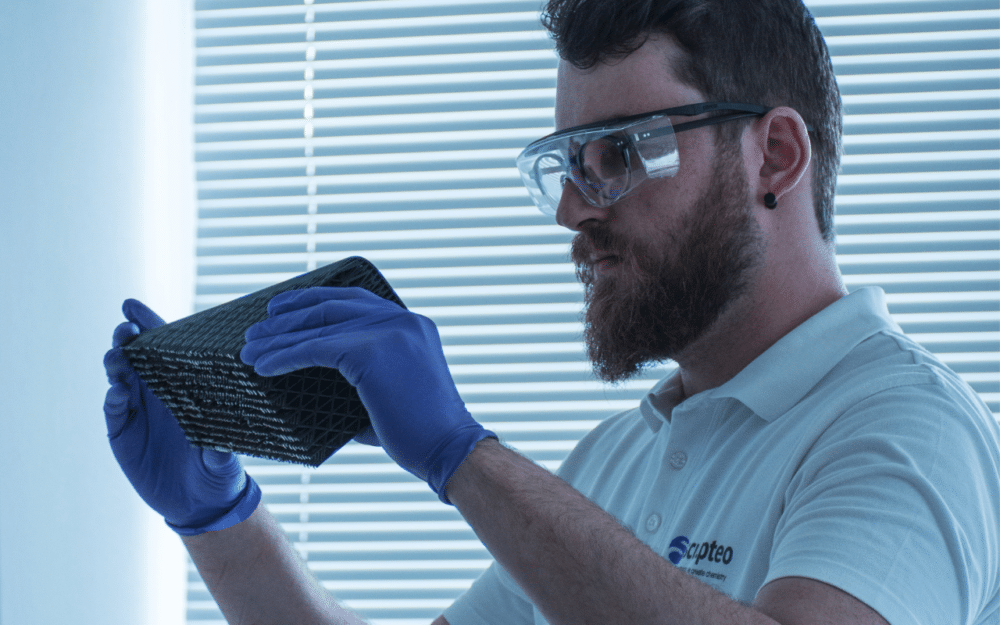
Could you elaborate on the rigorous processes Sculpteo implemented to meet the certification requirements?
Alexandre d’Orsetti: “To achieve ISO 13485 certification, Sculpteo implemented rigorous quality management processes, including comprehensive documentation and traceability systems, stringent testing and validation procedures, and continuous monitoring and improvement protocols. We established a robust risk management framework to identify and mitigate potential issues throughout the production lifecycle. Our team underwent extensive training to ensure adherence to these processes, and we conducted internal and external audits to maintain compliance with the highest standards of medical device manufacturing.”
How will Sculpteo maintain compliance and ensure consistent quality across its medical device manufacturing?
Alexandre d’Orsetti: “We will maintain compliance and ensure consistent quality by adhering to our established quality management system, which includes continuous monitoring and regular audits. We will keep up-to-date with regulatory changes and industry best practices, ensuring our processes evolve accordingly. Additionally, we will invest in ongoing employee training and advanced manufacturing technologies to maintain precision and reliability in our production processes. Customer feedback will be actively sought and incorporated to drive continual improvement.”
Could you share insights into any novel materials, medical devices, or manufacturing techniques Sculpteo is exploring?
Alexandre d’Orsetti: “We have been at Sculpteo, producing medical devices for a couple of years already, and the field of applications that we have identified are mainly in orthopedic devices, dental, and surgery assistance. We will be producing components for Class I and IIa medical devices mostly with our existing machines and mostly with powder bed technology machines. Those machines are the most suitable equipment for series production, and they are covered by the scope of our ISO13485 certification. The adoption of these technologies in the medical field is quite recent, so we will very likely develop tailored solutions, and discover new applications in collaboration with healthcare professionals.”
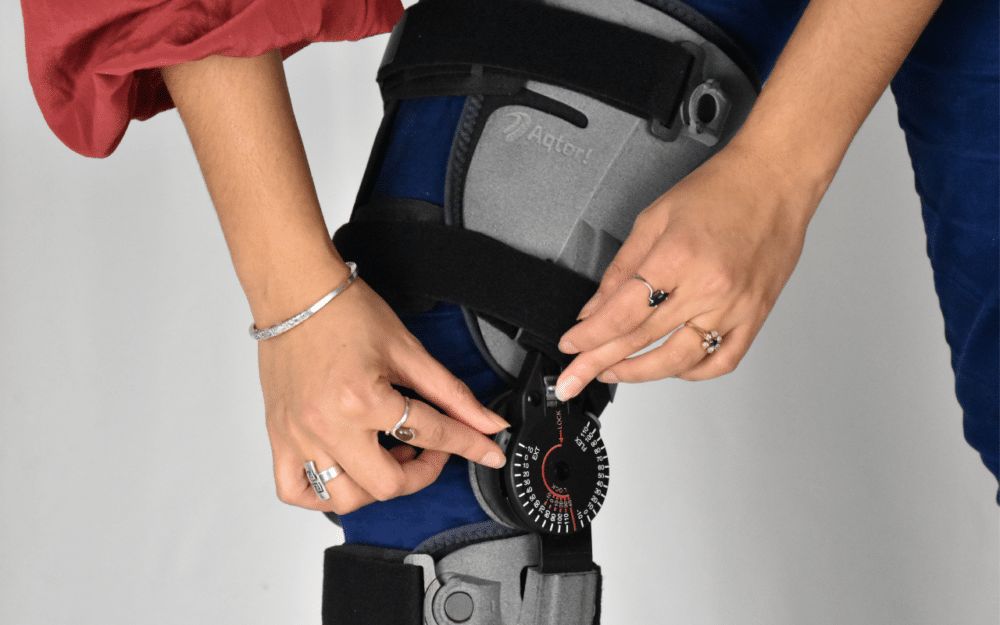
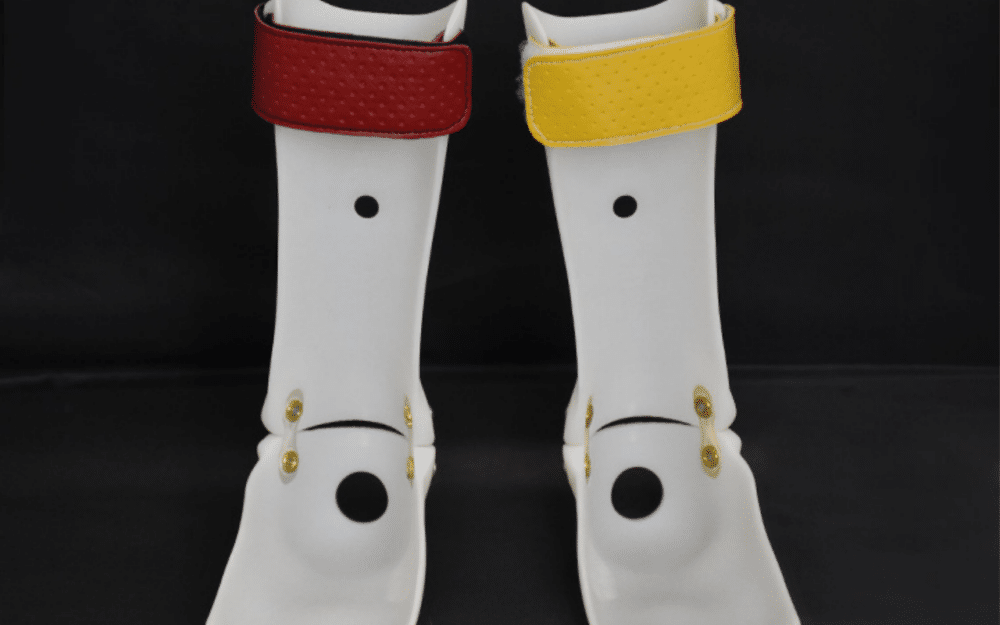
Are there any specific medical applications or use cases Sculpteo aims to address through its certified products?
Alexandre d’Orsetti: “Our certified products target several specific medical applications, including orthopedic devices, such as O&P (orthosis and prosthesis) for the lower and upper limbs. We focus on producing bespoke prosthetics to improve mobility and quality of life for amputees. Our design for additive manufacturing expertise, combined with our BASF forward AM service team allows us to design dedicated workflows such as lattice generation, to leverage end-to-end solutions from automatic 3D file generation to delivery. There is also a strong demand for surgery assistance devices, either to help prepare training for a surgical act or to produce tools during the surgery. These applications underscore our commitment to delivering tailored solutions that address the unique needs of each patient.”
How does the company plan to collaborate with healthcare providers and other stakeholders?
Alexandre d’Orsetti: “Sculpteo plans to collaborate with healthcare providers and other stakeholders through partnerships, joint research and development projects, and educational initiatives. We aim to work closely with surgeons, dentists, and medical researchers to develop and refine our products, ensuring they meet clinical needs. We see a huge opportunity in collaborating with industry experts to provide dedicated and automated workflows, leveraging our software and design generation capabilities. Additionally, we will participate in industry conferences and forums to share knowledge and insights, fostering a collaborative environment that drives innovation and improves patient care.”
Explore our other stories on 3D printing