Imagine a made-to-measure 3D-printed wheelchair “cool enough to go to the club with” and that would be a real “human body extension.” That’s what Layer, an industrial design agency based in the U.K., has tried to make with the GO project. Layer’s founder, Benjamin Hubert, talked to us.
ME e-mag: Why did you use 3D printing for the GO wheelchair?
Benjamin Hubert: The GO wheelchair is a particularly unique device—I would call it more a mobility device than a medical device. The project started by talking to wheelchair users a lot. We spent about six months just to talk to people. One of the insights that came out of that period was really about the fact that everybody has a different size, shape, weight, injury, physical condition and that what they need is a made-to-measure solution that will be just for them.
So 3D printing presented itself as an option to potentially do something that could be automated, use the physical form and shape of the human body and be represented in the product very literally. With 3D printing, we are using a sophisticated but automatically quite simple approach—taking data and transforming it into a piece of three-dimensional equipment. For this approach, we take your biometric scan—your physical shape—and then there is a consultation period because not everything is just about the human shape. It’s also about how you live your life, about how long you’ve had your condition, etc. That combination has been a really powerful tool to make something that is really a human body extension.
ME e-mag: Is everything 3D-printed?
Benjamin Hubert: The only two parts that are 3D-printed are the seat and the footrest. Every other component is the same on every chair. The only two components you need to change and to look at everybody’s shape are the seat and the foot rest because they basically control everything: height, weight, angle, leg length, feet size, etc. The advantage of the GO wheelchair is that it increases comfort, it reduces injury because when something is made specifically for you you’re not moving around in your seat, you can control the body a lot more.

ME e-mag: Does it also change the way people view wheelchairs?
Benjamin Hubert: Yes. A lot of wheelchair users were telling us that they don’t want a machine or a medical device. They want an extension of the body. It should be beautiful, it should be cool, it should express their style. The whole idea is that it’s a vehicle that they’re in all day so why shouldn’t it be cool enough to go to the club or to use in every occasion? That was one of the biggest frustrations [that came] out of our research project.
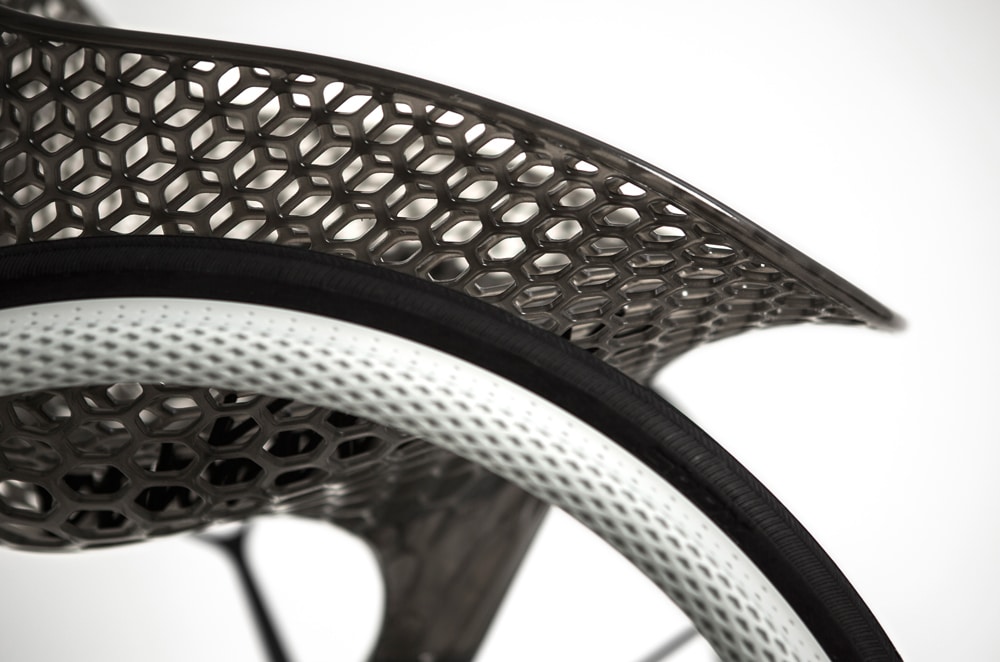
ME e-mag: What materials do you use to 3D-print the seat and the footrest?
Benjamin Hubert: The seat is a combination of different types of plastic resin. The footrest is 3D-printed titanium. It’s very strong and lightweight at the same time. The advantage when you 3D-print, for example, the footrest, is that inside it’s completely empty. Traditionally if you make that component it would be cast and it would be solid and much heavier. The goal is to go to full-scale production. We are talking to some companies at the moment, we’ll see how it goes.
ME e-mag: How long does it take to print this chair?
Benjamin Hubert: It only takes one or two days to actually put the parts but the process is a little bit longer. And of course it depends on where you are in the world and where you’re printing it, but the aim of the project is to dramatically reduce the amount of time it takes to manufacture a wheelchair. Because at the moment the whole process is very long and quite old-fashioned.