3D printing was once again a big topic at this year’s MEDICA trade show. We talked to Michael Gaisford, Director of Healthcare Solutions at Stratasys, to discuss the latest innovations in printers, materials and softwares as well as the benefits for healthcare. He told us about the new partnership between Stratasys and Materialise that will be a game changer.
MedicalExpo e-magazine: What is more important in 3D printing for Stratasys the hardware or the software?
Michael Gaisford: Stratasys is both a printer and a material company. Certainly the printers and the hardware are very important to us but what really drives our value proposition is the material: What capabilities can you create? Are they clear, are they flexible? What can you do with material in order to power various medical applications? Then of course you need to have the softwares to run the printers and we do have that too. Stratasys has a lot of software tools to operate our printers at peak performance. We do not have the software that converts a MRI-CT to a 3D printed model, but we have partnered with others in that field.
MedicalExpo e-magazine: What kind of new partnerships with software companies are you planning?
Michael Gaisford: We will announce at RSNA a brand new collaboration with one of the leaders of software providers in 3D printing: Materialise. In March 2018, Materialise had gained an FDA clearance for their software Mimics inPrint to be used to create 3D printed models for diagnostic purposes. Meaning that a doctor can rely on the actual 3D printed model to make decisions about patients there. This is very important because in the past the FDA cleared only the software but now with this decision the entire process is cleared.
“At RSNA we’ll be announcing an extension of the printers and materials that are covered by the clearance. Materialise will be able to use the Stratasys J750 as well as the Objet 30 Prime.”
This is a very big advancement for us to provide our customers with the assurance that they can trust the solution they’re adopting to aid in patient care.
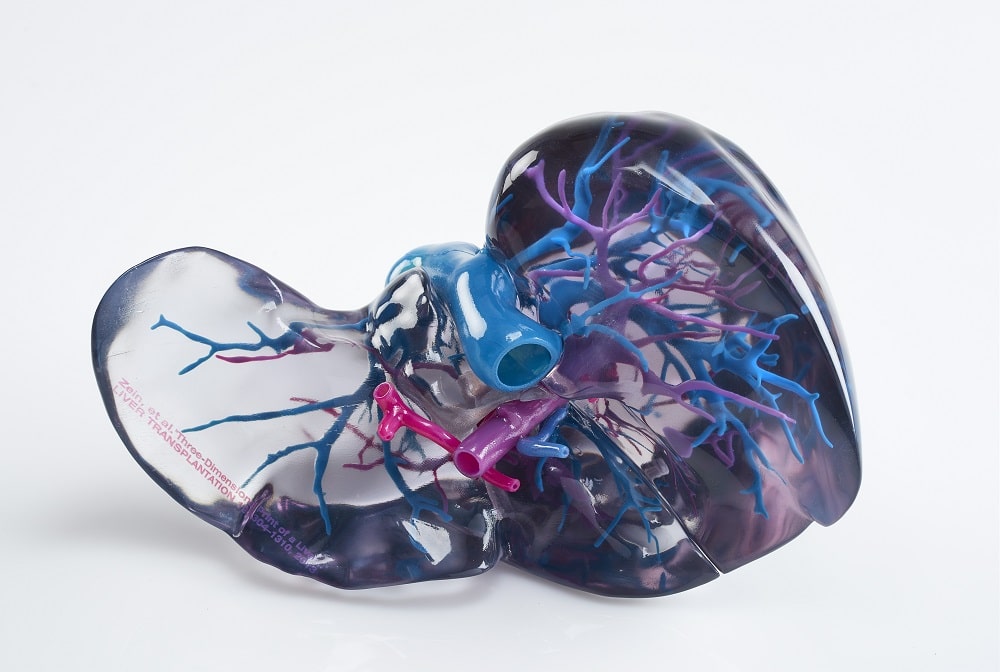
MedicalExpo e-magazine: What are the latest innovative features of the J750 printer?
Michael Gaisford: There are several reasons the J750 is the best 3D printer for medical models. And now that it is part of the FDA-cleared solutions for printing models for diagnosis use, the advantages are even more clear. The J750 is ideal for medical modeling because of its unrivaled versability. It runs six different materials including a variety of colors and transparency, and materials that can have flexibility as well. Because of this, you can support models across a wide range of anatomy and applications.
“It is the only printer that has the ability in a single part to combine rigidity and flexibility, and color and transparency. Most printers out there can print only a single material and most often they are very rigid models.”
Single material can be appropriate in certain applications, but it is unable to meet a wide array of applications that require the sophistication of multi-material. For example, let’s think about more complex programs such as surgical oncology where you want to be able to print a kidney and the tumor that’s inside of it and the biliary duct and the arteries and veins and other critical structures, and you want to be able to see each of them differently. How can you do that with a single-material-rigid printer? It can’t be done.
So with the Stratasys J750, you can create models that are functional for pretty much every therapeutic area in a hospital: you can create very large models like a pelvis, small models like a single valve, flexible models that replicate the human heart’s tissue properties, rigid models that replicate bones, and you can combine them.
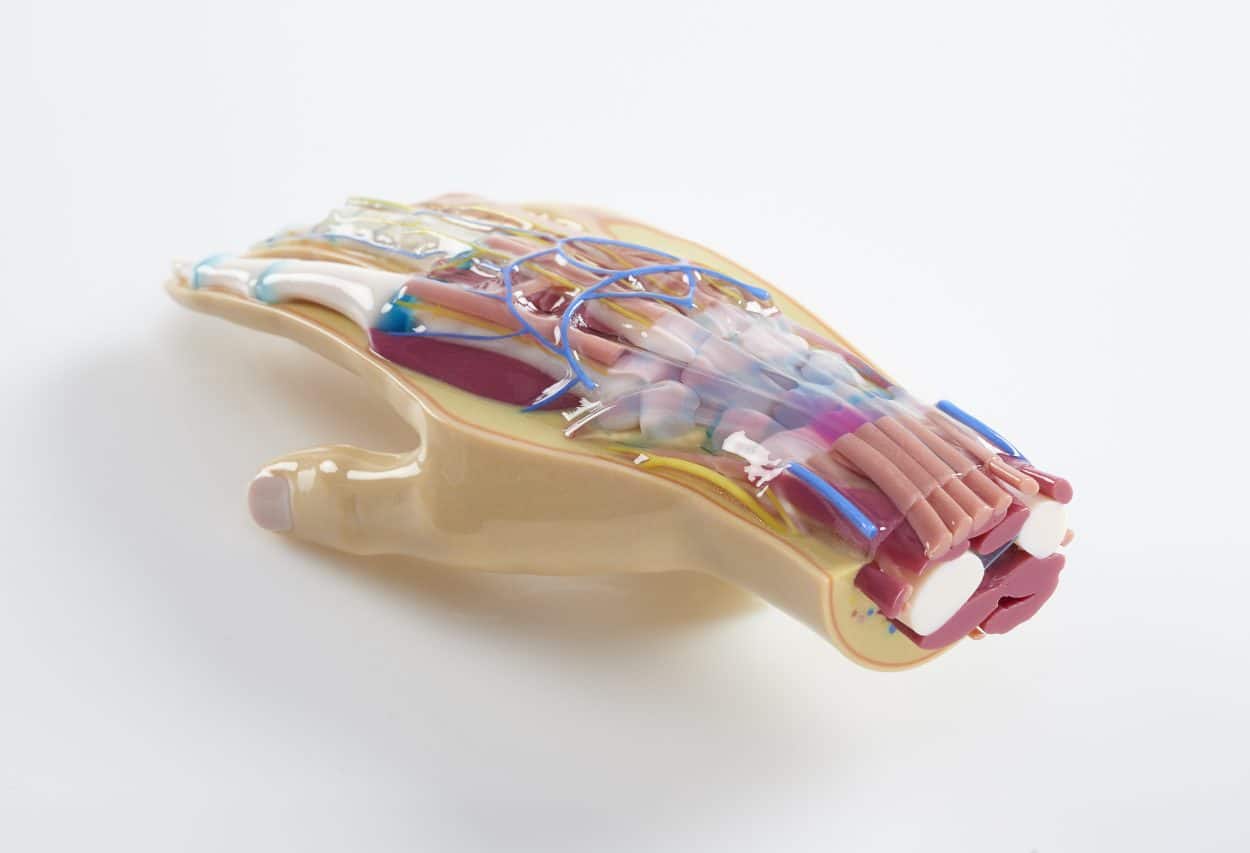
MedicalExpo e-magazine: What about the different colors? How are they useful for the surgeon?
Michael Gaisford: On a human model, you might print the kidney clear, and the tumor on the inside will be printed in green and then the biliary in yellow, the arteries and veins in red and blue. So you can use all those colors throughout the transparency.
Or for a brain tumor surgery, you might print a brain in a flexible transparent material, the tumor in green, nerves and arteries and veins in different colors as well, and then the surgeon uses the flexible model and can actually operate on it. He can explore how he’s going to reach the tumor without damaging the brain tissue, he’s able to do that because it’s a flexible model that he can manipulate with a tumor that he can clearly see, and arteries and veins that he can also clearly see, and of course a rigid skull.
“Being able to incorporate all of these things makes a very powerful model that can become not only a model that you can visualize and look at, but a functional model that you can operate on, practice on, do the trial on.”
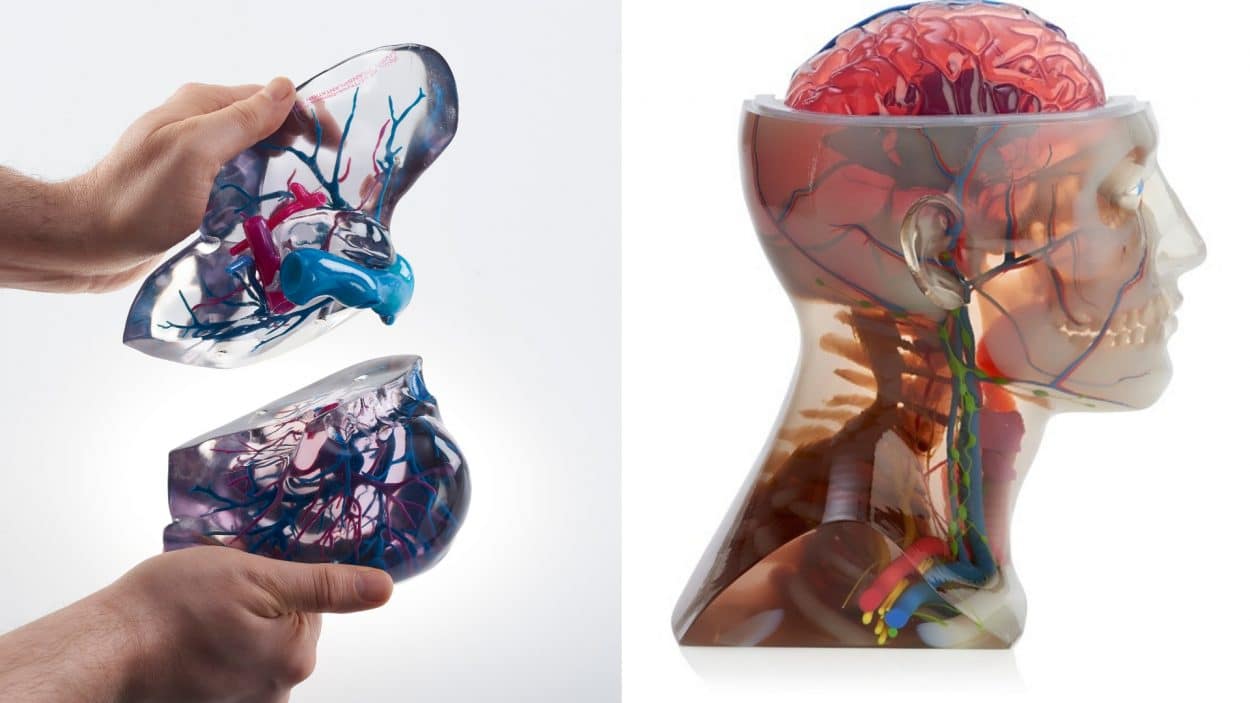
MedicalExpo e-magazine: Do these functional 3D printed models that you can operate on improve surgical outcomes?
Michael Gaisford: Absolutely. If you’re treating a patient with a broken leg, you’re not going to print their bone. Doctors know how to treat it, they do it every day and it’s a very simple procedure so what do they need a 3D printed model for?
But if you are doing a transaortic valve repair on a patient with a complex anatomy, printing a model and evaluating it ahead of time allows you to prepare a clear plan of action, make critical decisions prior to the surgery so you’re not spending time evaluating and analyzing in the operating room. So for the most complex and challenging procedures, there is a wide and critical number of cases demonstrating the benefits of 3D-printed models.
“For example, for pediatric heart patients, they found that patients recovered much faster and were released from the intensive care unit much faster. One study demonstrated 40 hours fewer in the ICU when the 3D-printed model was used.”
Can you imagine a family’s relief when their child is no longer in the ICU? It’s a sign of strong recovery. It’s almost two days shorter in the ICU where it is also very expensive to take care of patients. This interest in the academic side is a sign of the growth of medical 3D printing: there is more and more published literature about it.
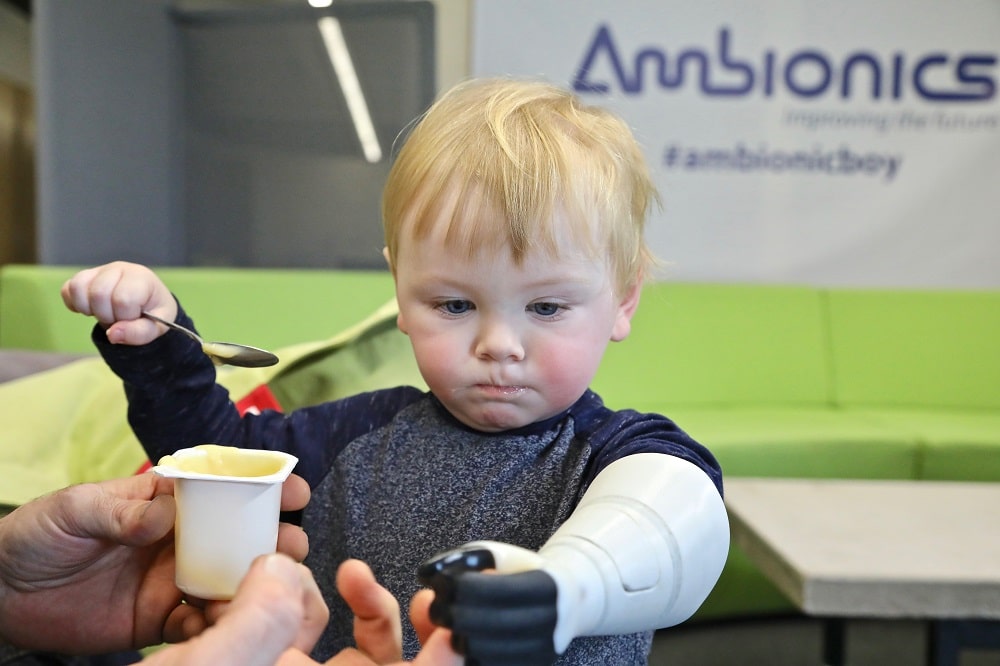
MedicalExpo e-magazine: What are the latest innovations in 3D-printed prostheses?
Michael Gaisford: It really ranges for different applications. One of the applications that gets the most credit is when you print a robotic arm for a child. Because that population is very underserved today. The cost of a prosthesis is tens of thousands of dollars, a family just can’t afford that especially because their child is going to outgrow it in two or three years. So 3D printing has really democratized prostheses for younger patients. Some groups are also adding bionics and mechanical functions in order to improve the arm functionality.