A tiny robotic assistant that weighs no more than a coin and can perform precise surgical tasks has been developed using origami-inspired bonding technology. It can be used in minimally invasive surgery to avoid excess force on the incision site.
Robotic surgical assistants are commonly used to improve precision and control during laparoscopic procedures, where tools and a mini camera are inserted into small incisions, typically in the abdomen. However, as they are operated by complex internal mechanisms, the devices need to be quite large, which can be obtrusive in the operating room. They are also limited in terms of what procedures they can assist with and are unsuitable for use on fragile tissue.
Researchers from Harvard’s Wyss Institute and the Sony Corporation have now invented a new technique that can produce a miniature remote center of motion manipulator (RCM), that allows for a robot that is small in size and precise in action.
The mini-RCM weighs 2.4 g and measures 50 mm × 70 mm × 50 mm. It successfully performed a difficult mock surgical task in a recent trial, the results of which were published in the journal Nature Machine Intelligence. Like the Japanese paper art of origami, the “Pop-Up MEMS”’ method involves bonding layers of materials so that they can unfurl from a flat starting shape into a more complex structure, allowing for a smaller RCM.
The mini-RCM is controlled by three linear actuators (mini-LAs) that allow it to move in multiple dimensions and help correct hand tremors and other disturbances during teleoperation. It is made by layering several laser cut materials to create a dense, flat plate that “pops up” into the complete electromechanical structure.
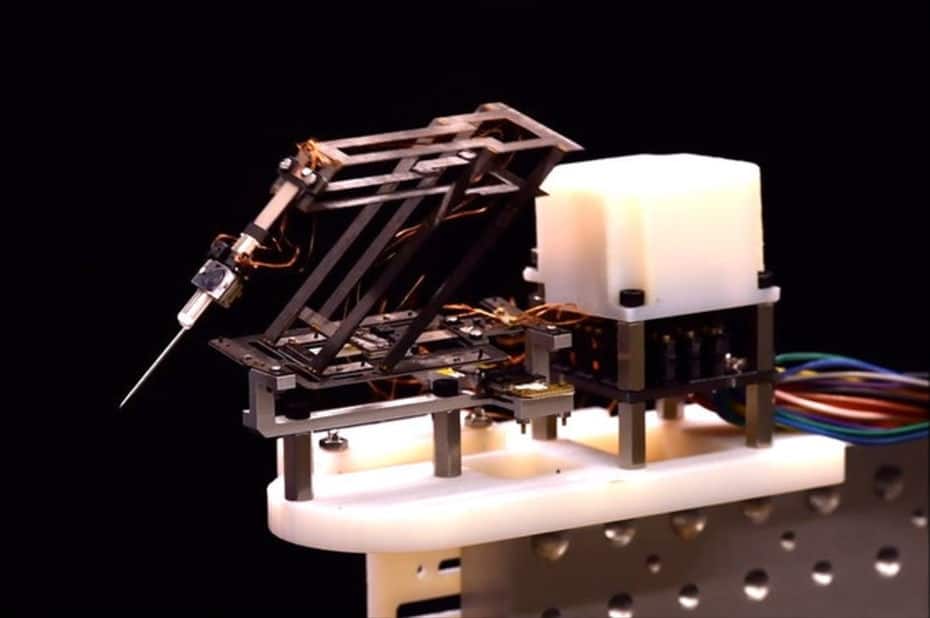
As the manufacturing technique is fairly simple and does not involve bringing together tiny parts, the mini-RCM is a much cheaper and accessible option than micromechanical devices. It is also easy to set up and install and the robot can be easily removed from a patient’s body by hand, in the case of a complication or electrical outage.
Reducing Errors
The work is the fruit of a collaboration between Wyss Associate Faculty member Robert Wood, Ph.D. and Robotics Engineer Hiroyuki Suzuki of Sony Corporation. To test its efficacy the team connected the mini-RCM to a Phantom Omni device—commonly used in surgery—which manipulated the mini-RCM in response to the movements of the surgeon’s hand. The mini-RCM tests dramatically improved user accuracy, reducing errors by 68 percent compared to manual operation. Dr Wood said:
“The Pop-Up MEMS method is proving to be a valuable approach in a number of areas that require small yet sophisticated machines, and it was very satisfying to know that it has the potential to improve the safety and efficiency of surgeries to make them even less invasive for patients.”
The researchers are now aiming to increase the strength of the robot so it can be used in more complex operations. Don Ingber, founding director of the Wyss Institute, added:
“This unique collaboration between the Wood lab and Sony illustrates the benefits that can arise from combining the real-world focus of industry with the innovative spirit of academia, and we look forward to seeing the impact this work will have on surgical robotics in the near future.”